Including the Kitchen Sink - Making and running it.
I got into the race, then I had to build the darn thing...
Here we go...
So, with a full BOM, I started getting materials and quickly ran into an issue of work space. I have a 50 sq/ft. space that I usually work out of at the Artisans Asylum, which suits me well for most of the things I work on. A larger project like this however, need a bit more room. So I picked up a space for it.
And from there I got to cutting stock. First up were the gear assemblies, made using the excellent gear generator by Matthias Wandel, which I needed to get working together properly to verify that it was all going to run like expected. The main bodies of these were based around the large gears, which were primarily made of x3 stacked layers of 1/4" MDF laminated together to make some super stout gears. I used 1/4" rather than 3/4" so I could use the laser cutter and cut out the gears in a very precise way.
Cutting one of the large gears.
After I got the gears in a solid state and printed off the pieces I needed, I could work on putting together the full axle assemblies. Each gear-set ran on an aluminum tub that was centered between 2 bearings, making it so all the pieces that stacked to make an assembly would run parallel.
These required a lot of printing, with some pieces taking a day and a half to print, with quite a few hours going into post processing the prints. This print alone took over a half a roll of filament on its own.
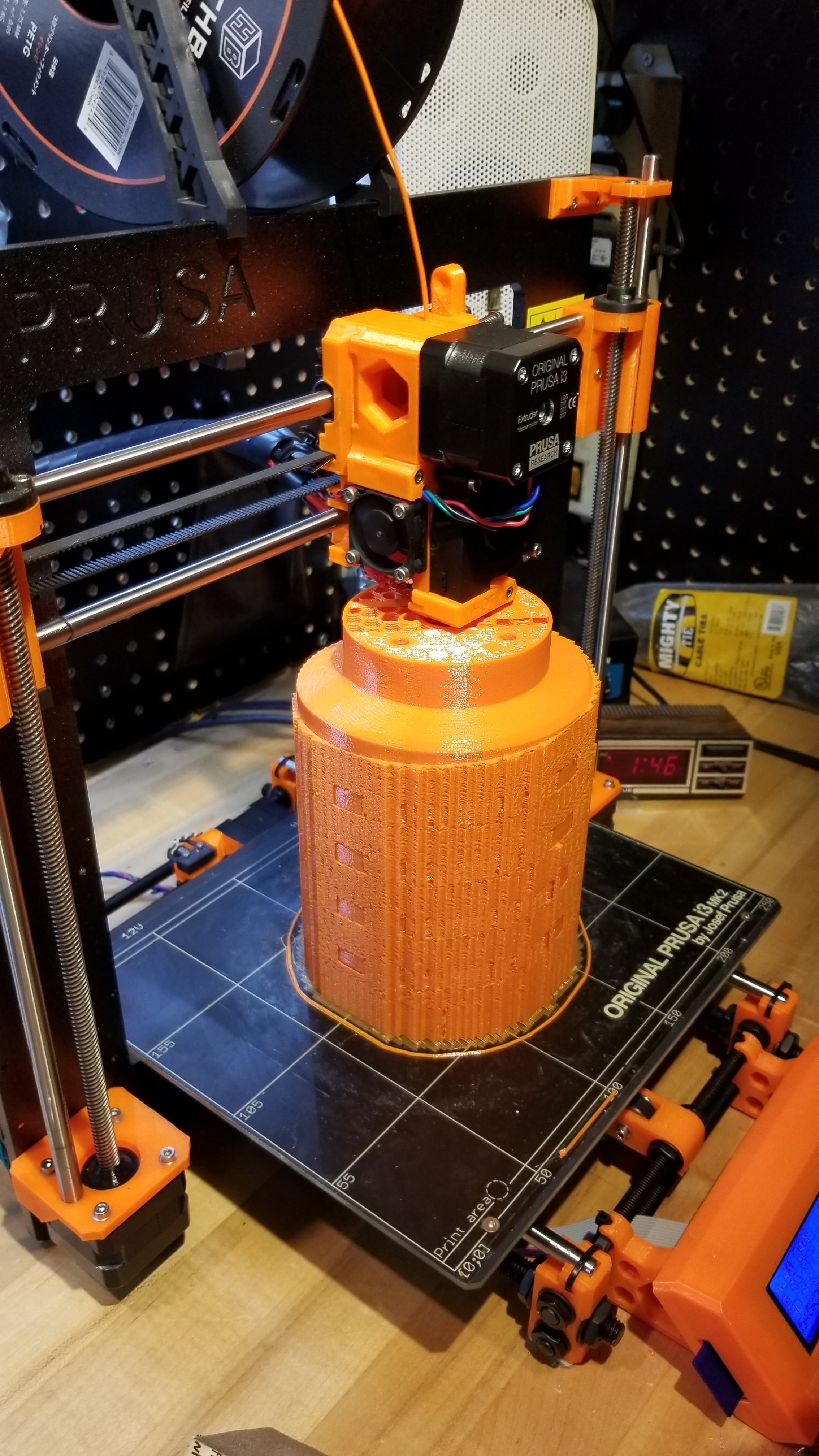
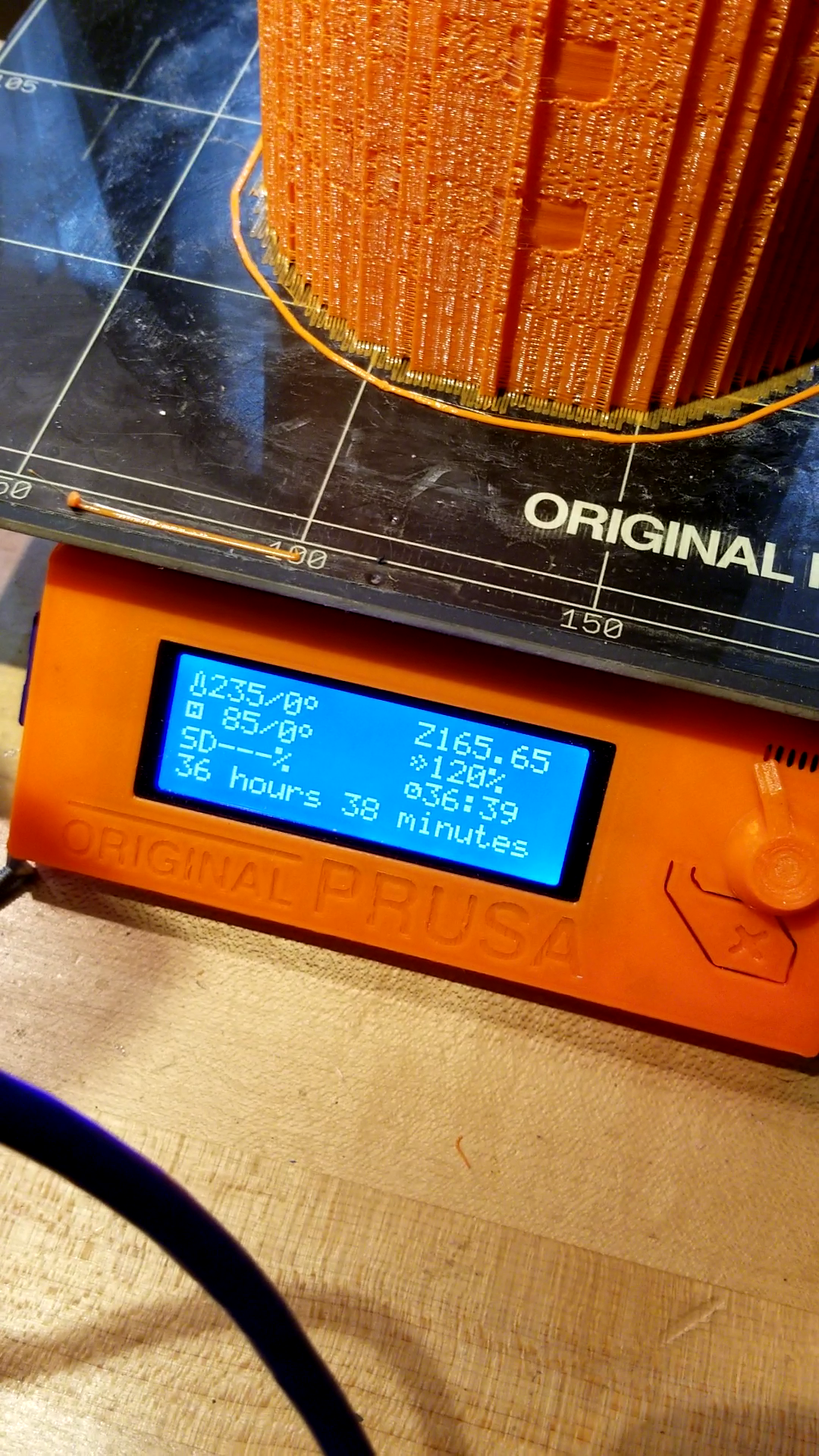
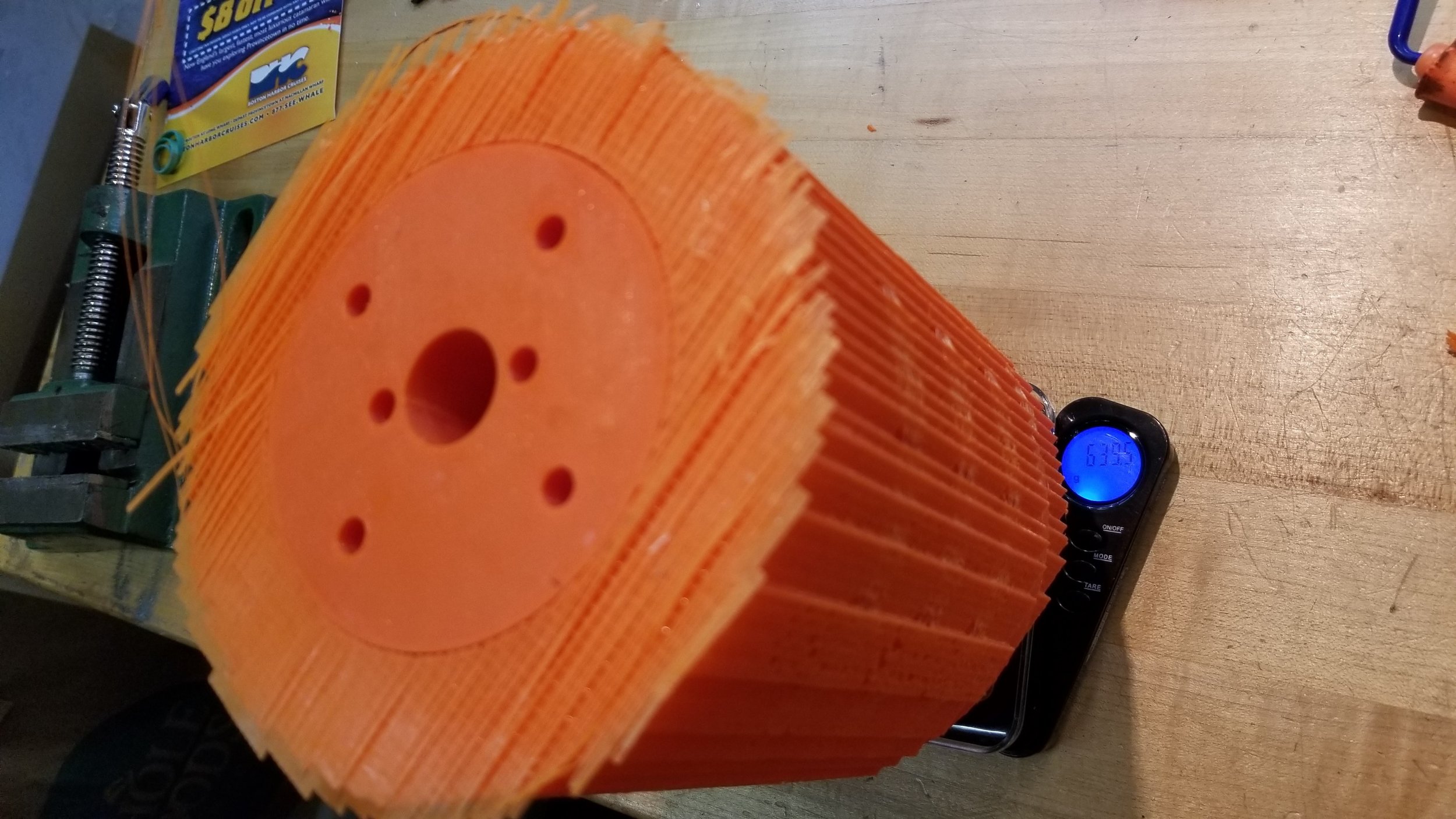
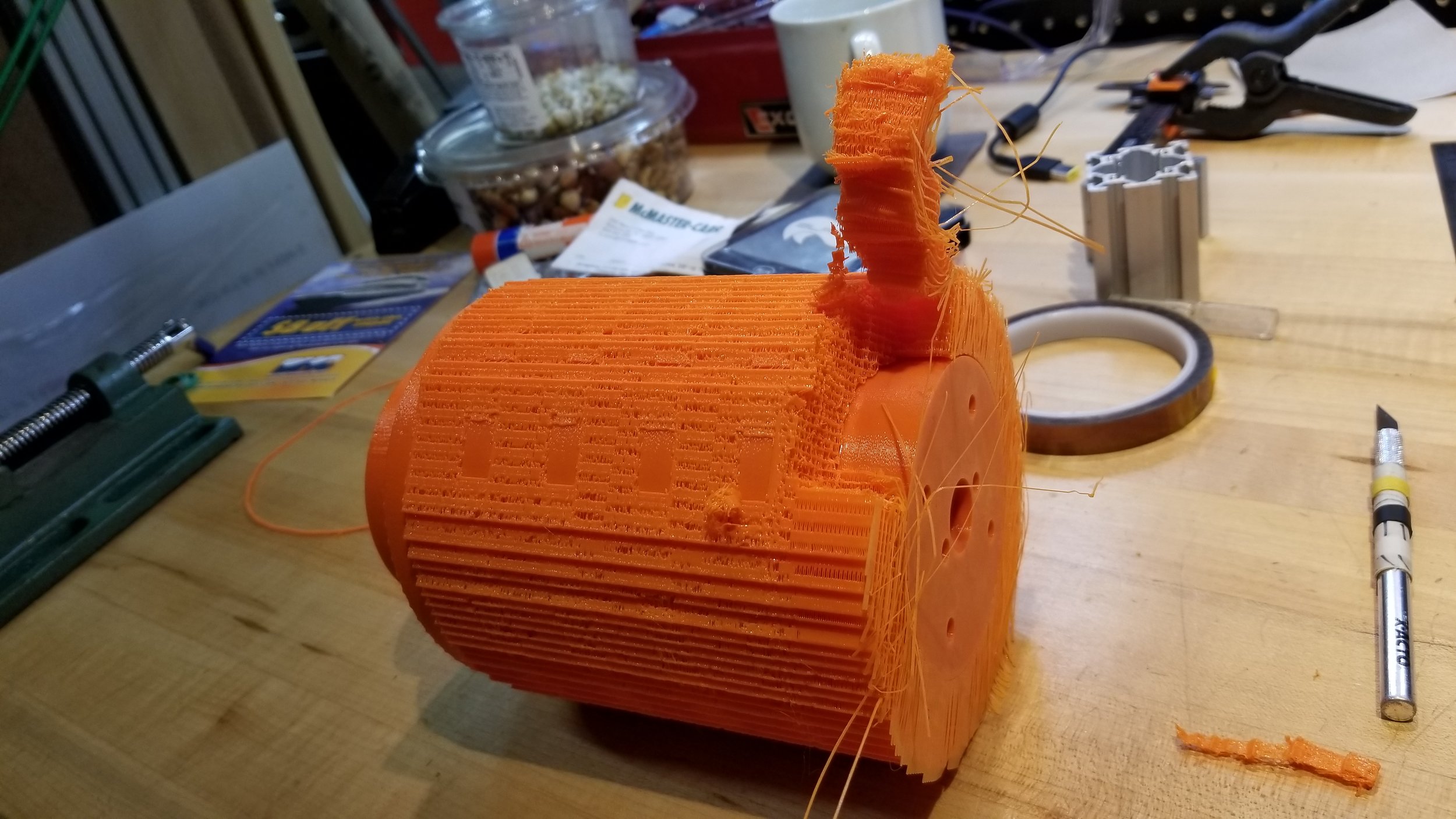
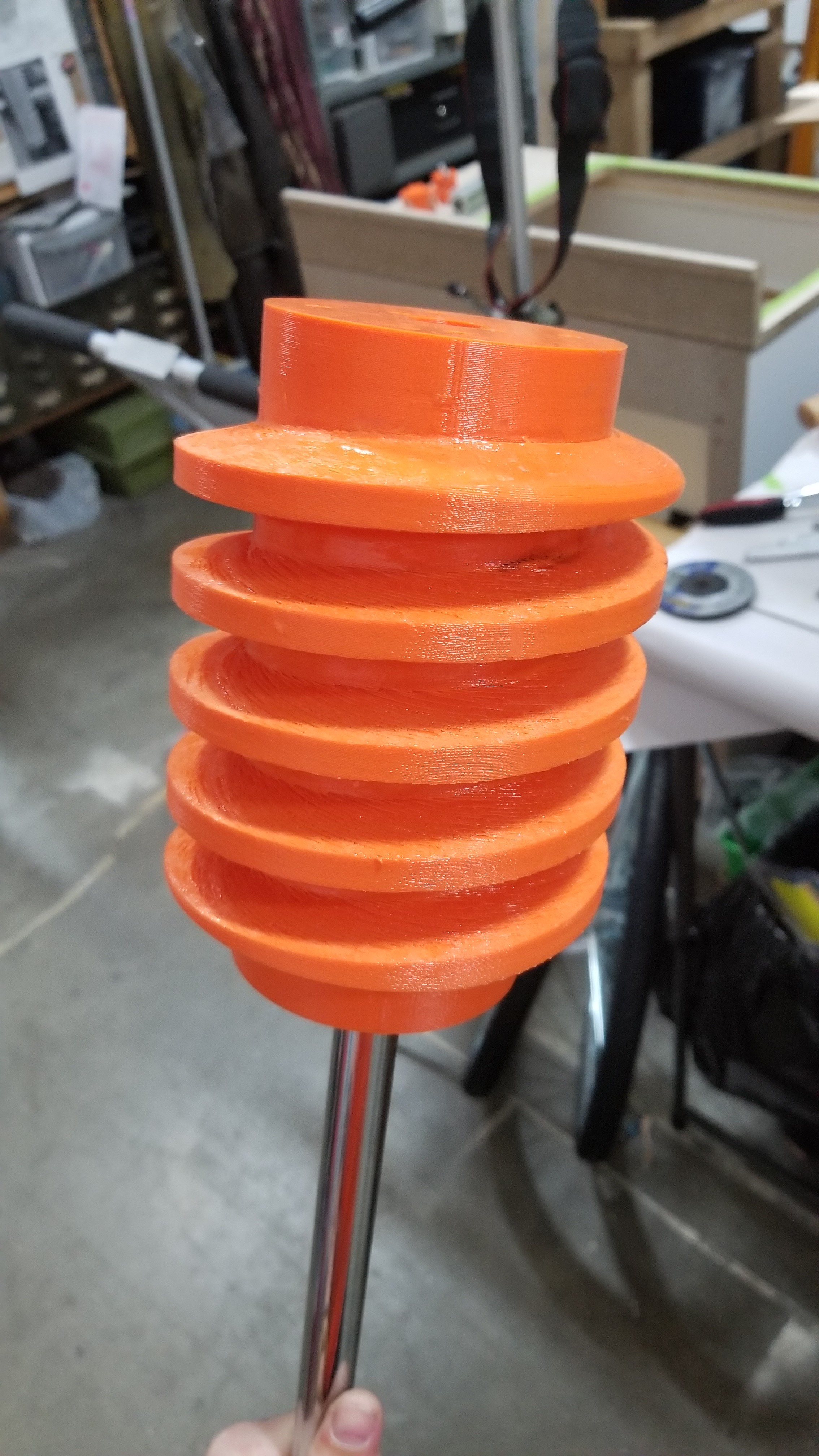
A lot of work went into each printed part.
Assembling it all and testing.
They work.
Due to the time left I had to work in parallel on assembling and readying the cabinet and countertop to be able to move at ~7mph and handle bumps.
The cabinet was a standard size from Home Depot that I was able to buy pre-assembled. It however was nowhere near road-ready as a large portion of the cabinet was held together with stapes. In addition it was also missing the countertop and the sink was not installed. No matter, I got to learn a pinch of cabinetry…
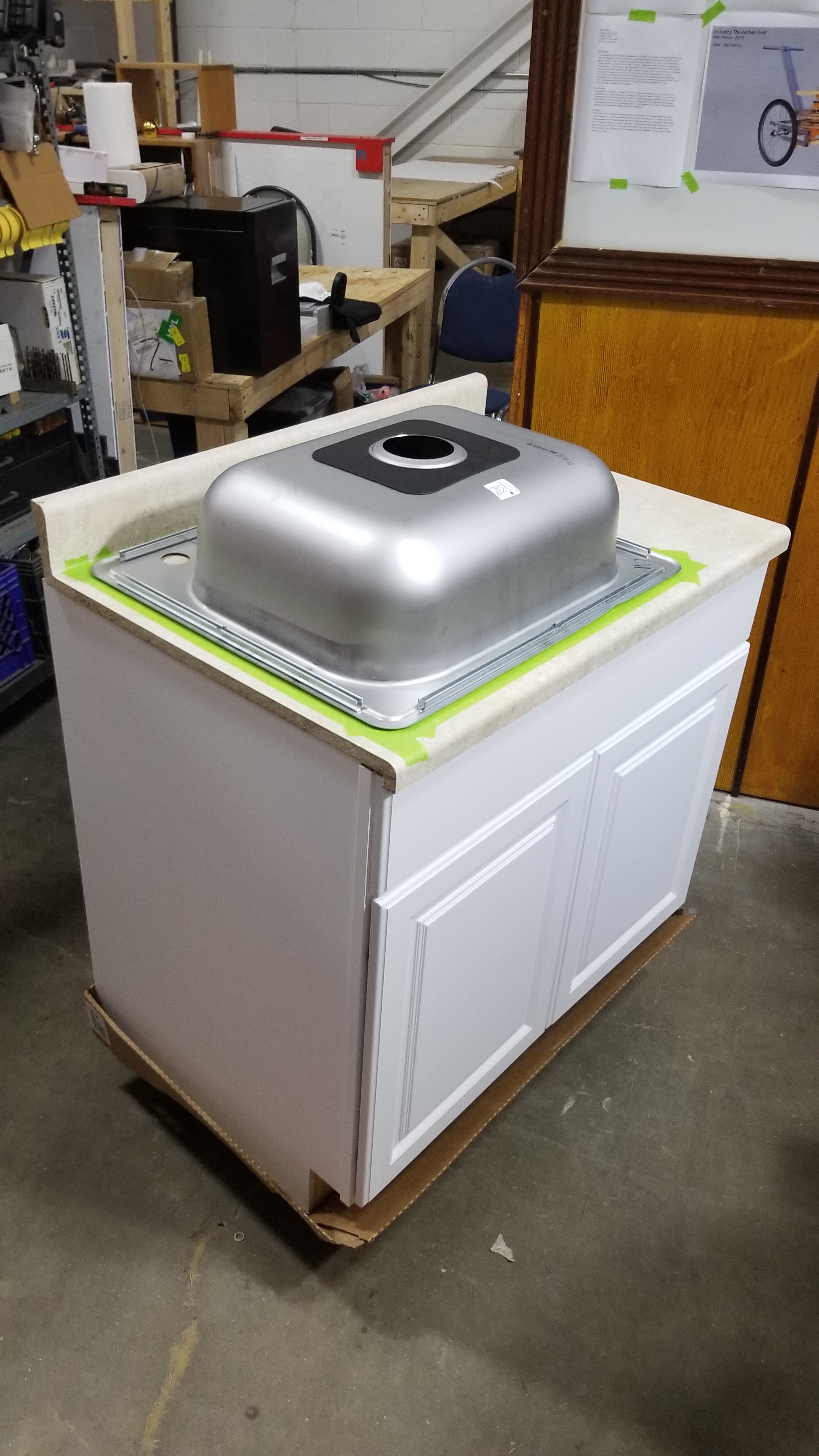
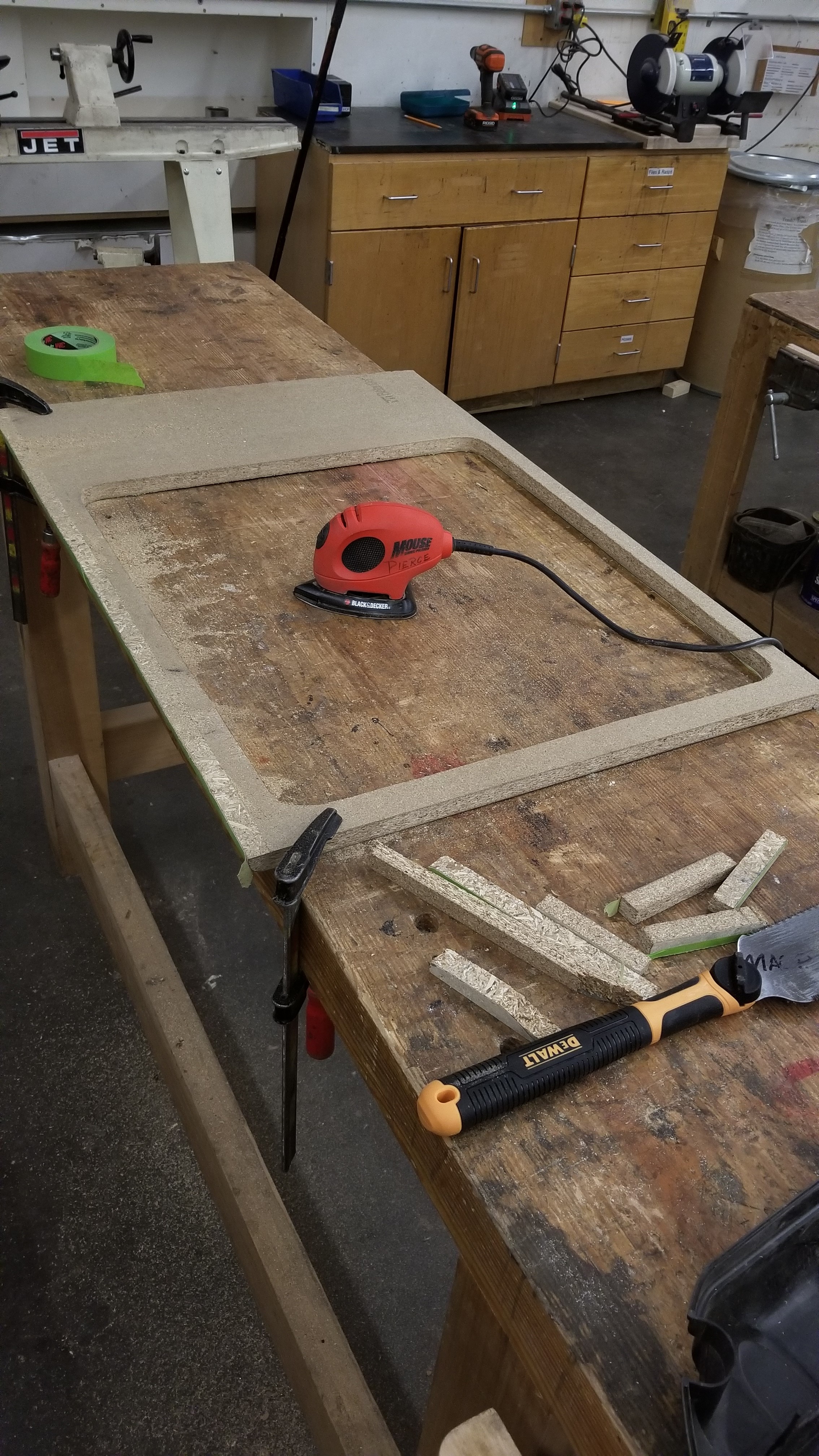
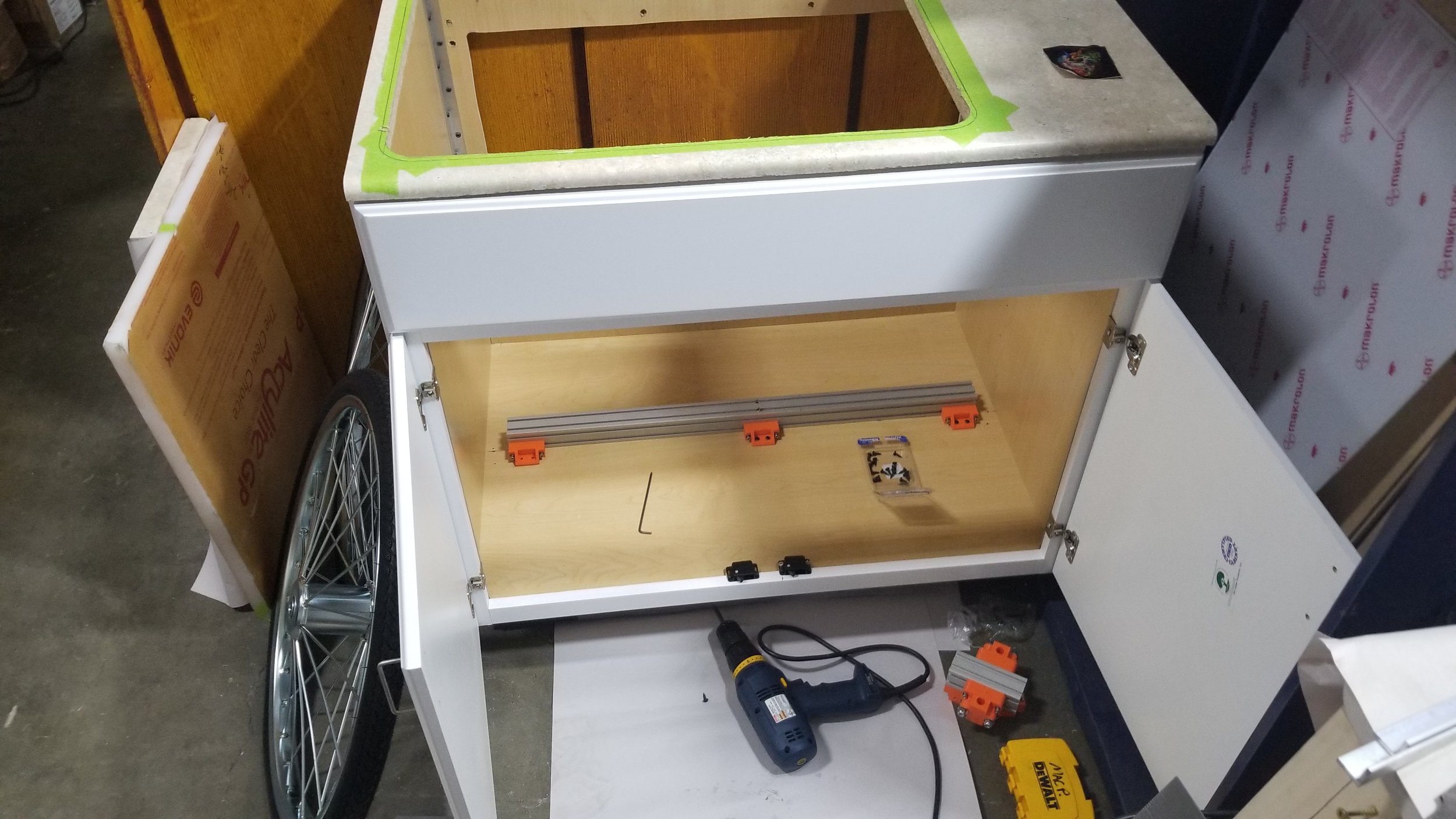
(Not shown, the aluminum framing needed in all the vertical corners of the cabinet.)
Q: So then, it’s going to be a cart, right? Don’t carts need handles?
A: Yes, yes they do. They need specially designed, welded aluminum handles.
Q: Do you know how to weld aluminum?
A: Ahaha, nope. But I’ll figure it out.
I was fortunate enough to be able to learn Aluminum MIG welding through the shop supervisor at work. All and all pretty easy once you learn how to deal with jams in the wire feeder…
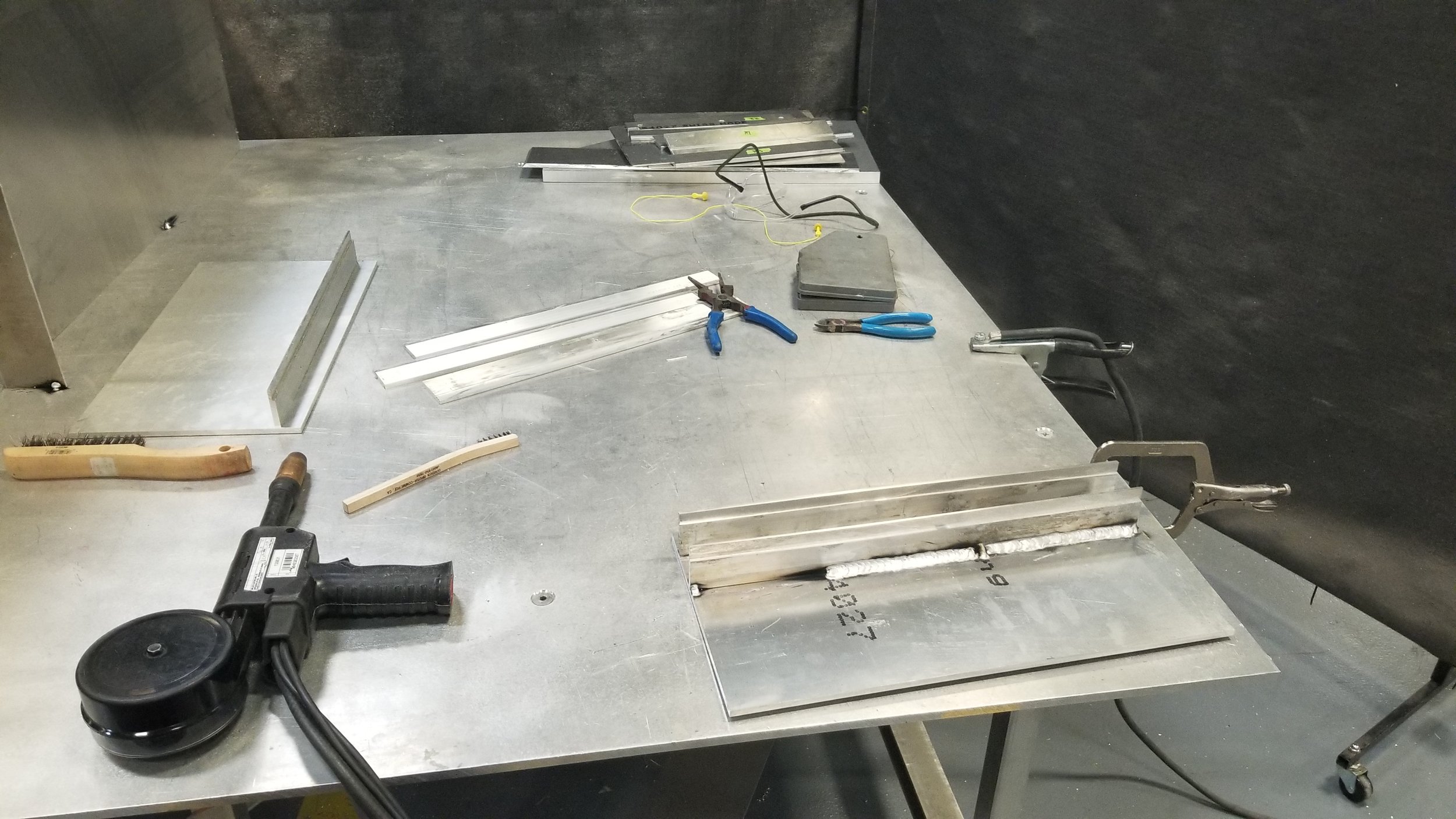
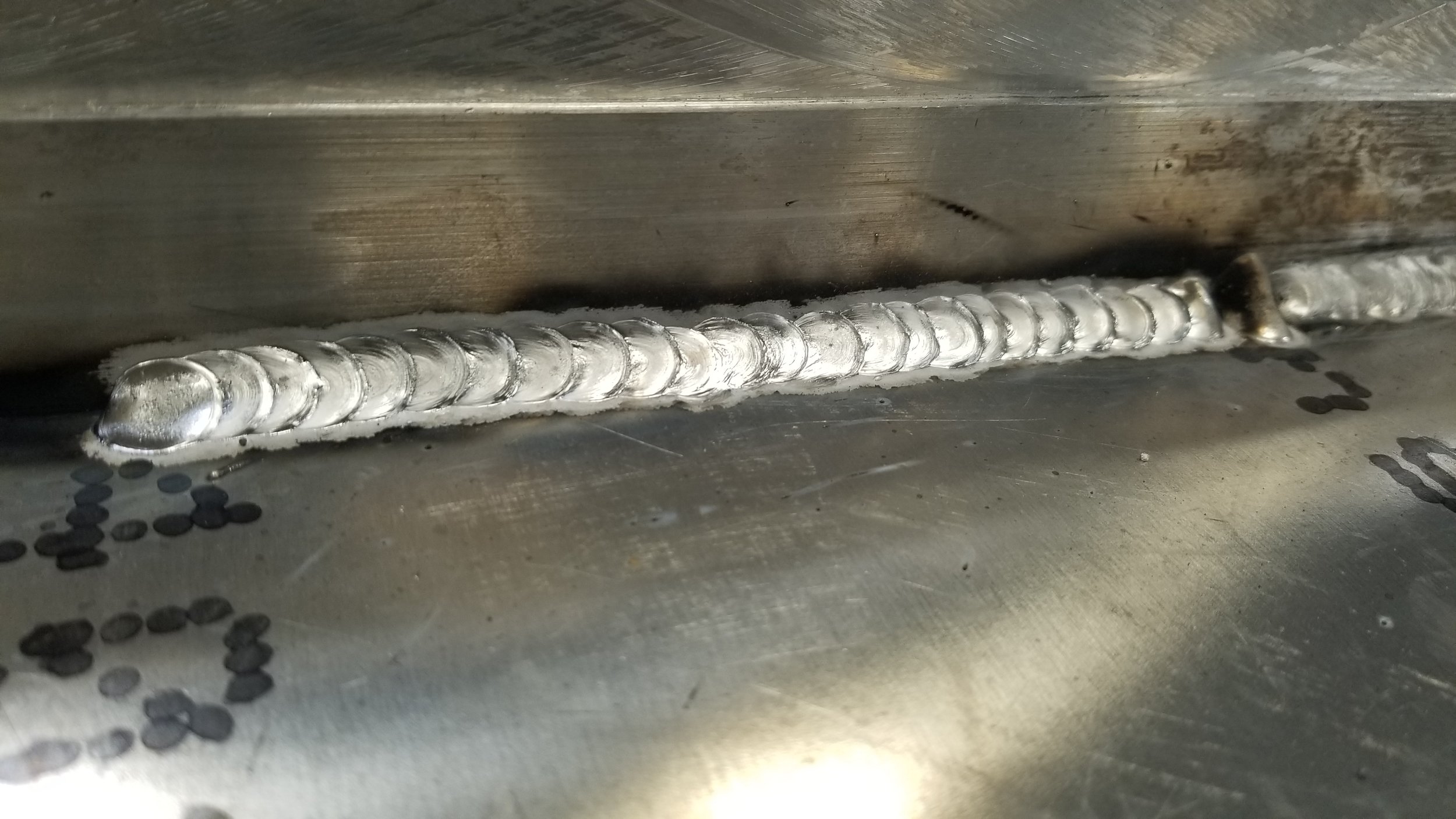

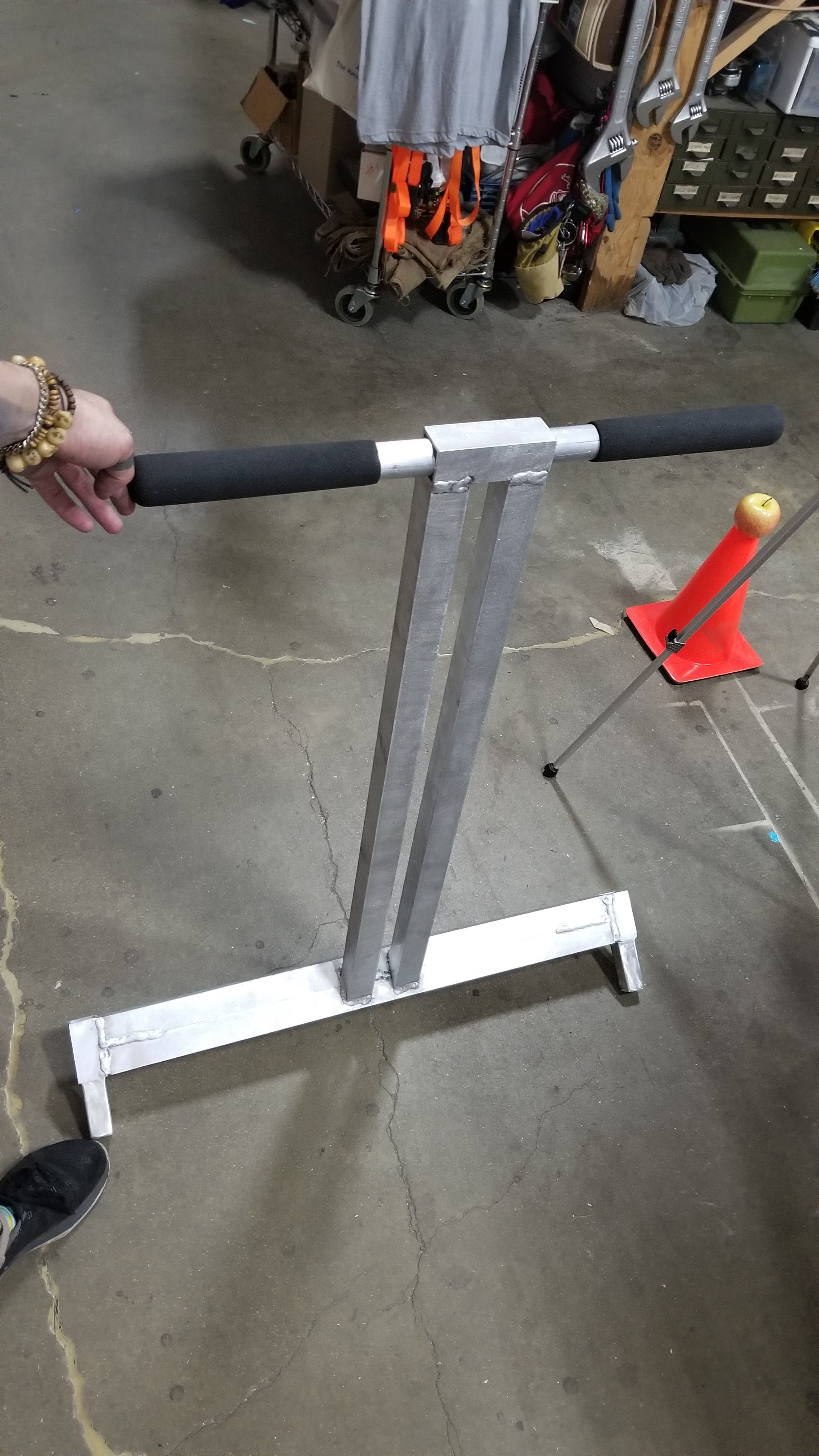
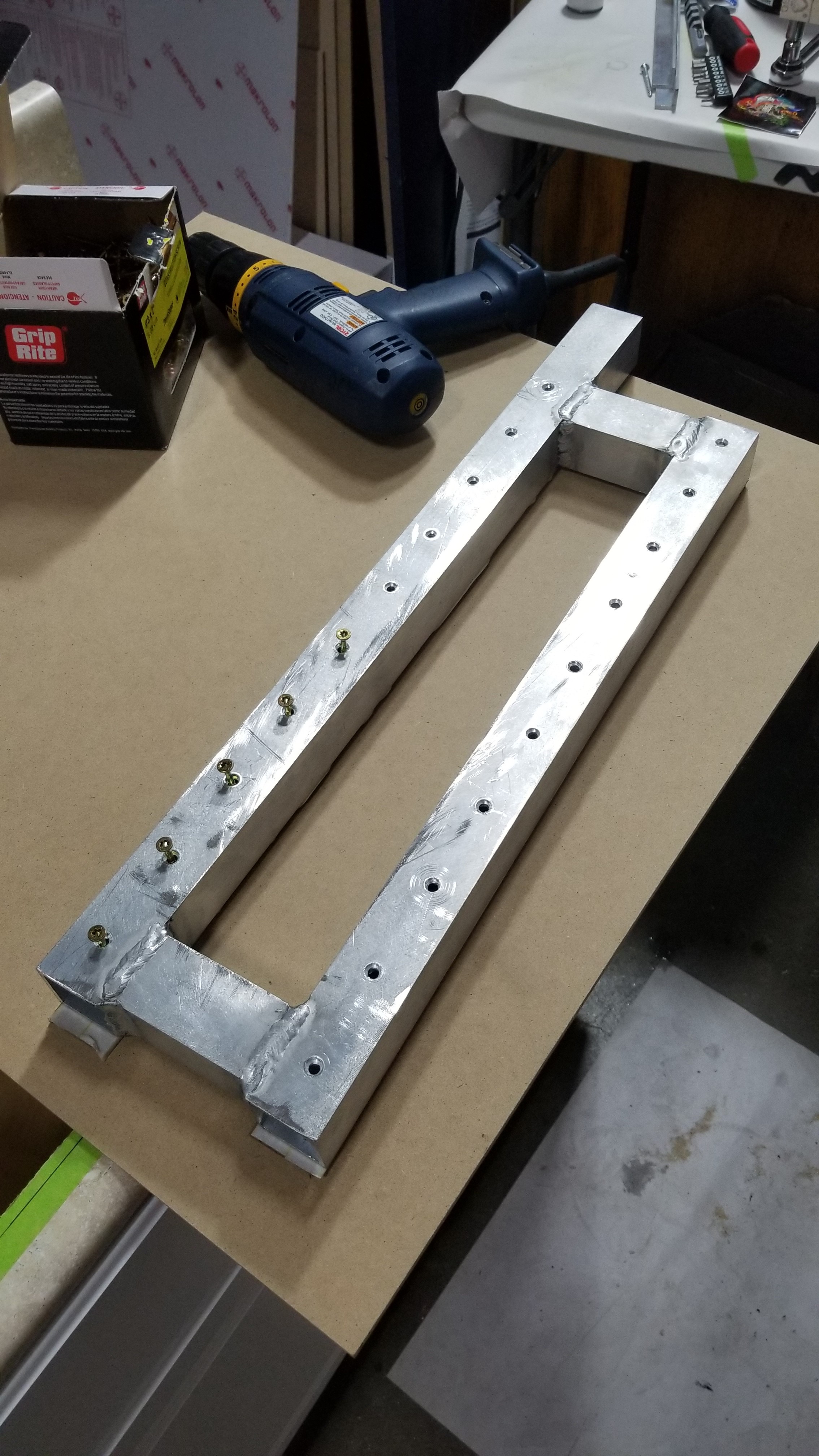
With all the component parts finished I was able to work on final assembly and testing.
At this point I’d like to stress how thankful I am that I’d modeled it all in Fusion 360 beforehand, as the assembly was a breeze after having made all of the components to spec. Other than needing to add in extra screws in a few parts and aligning, everything fit together very well.
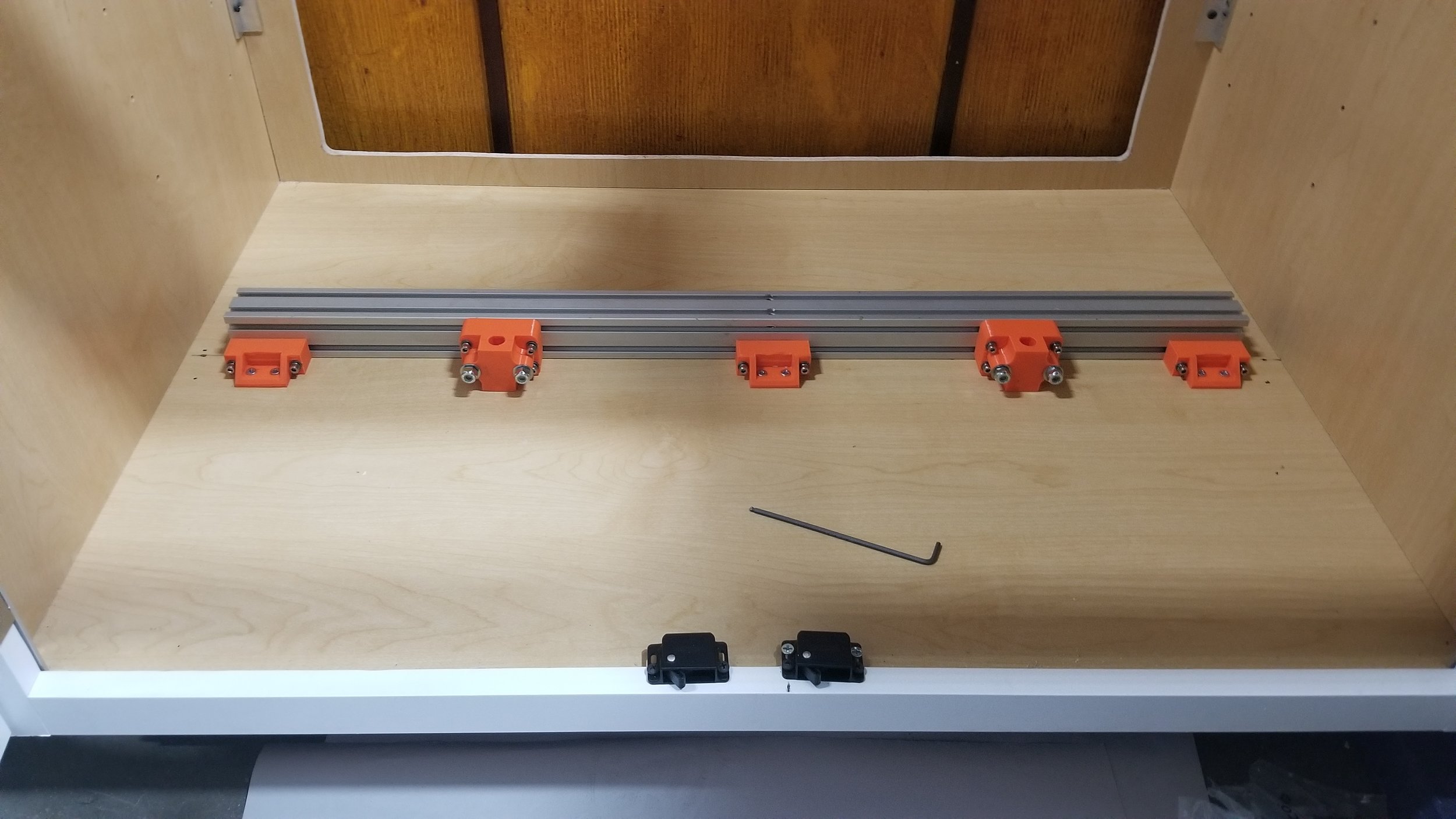
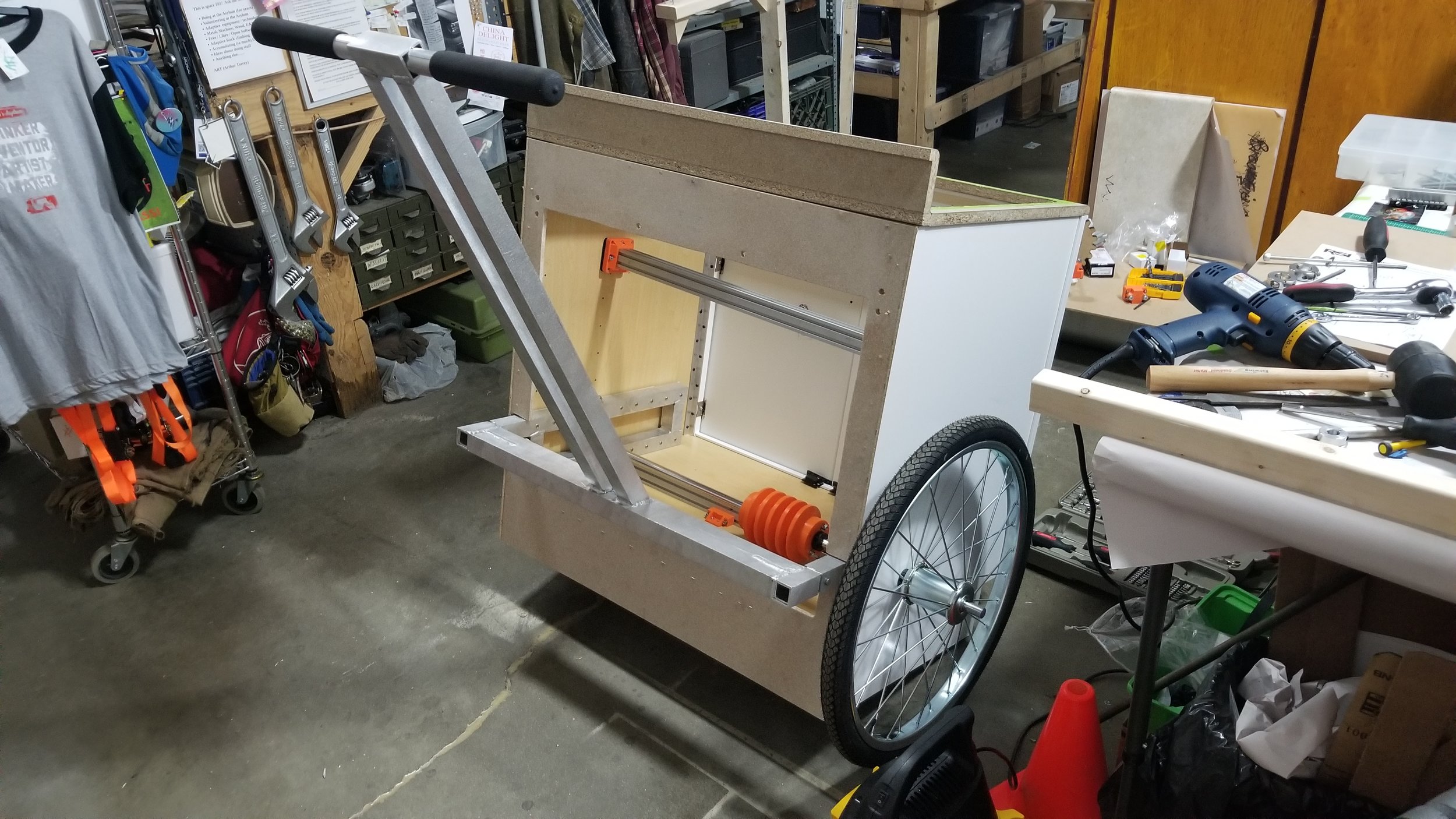
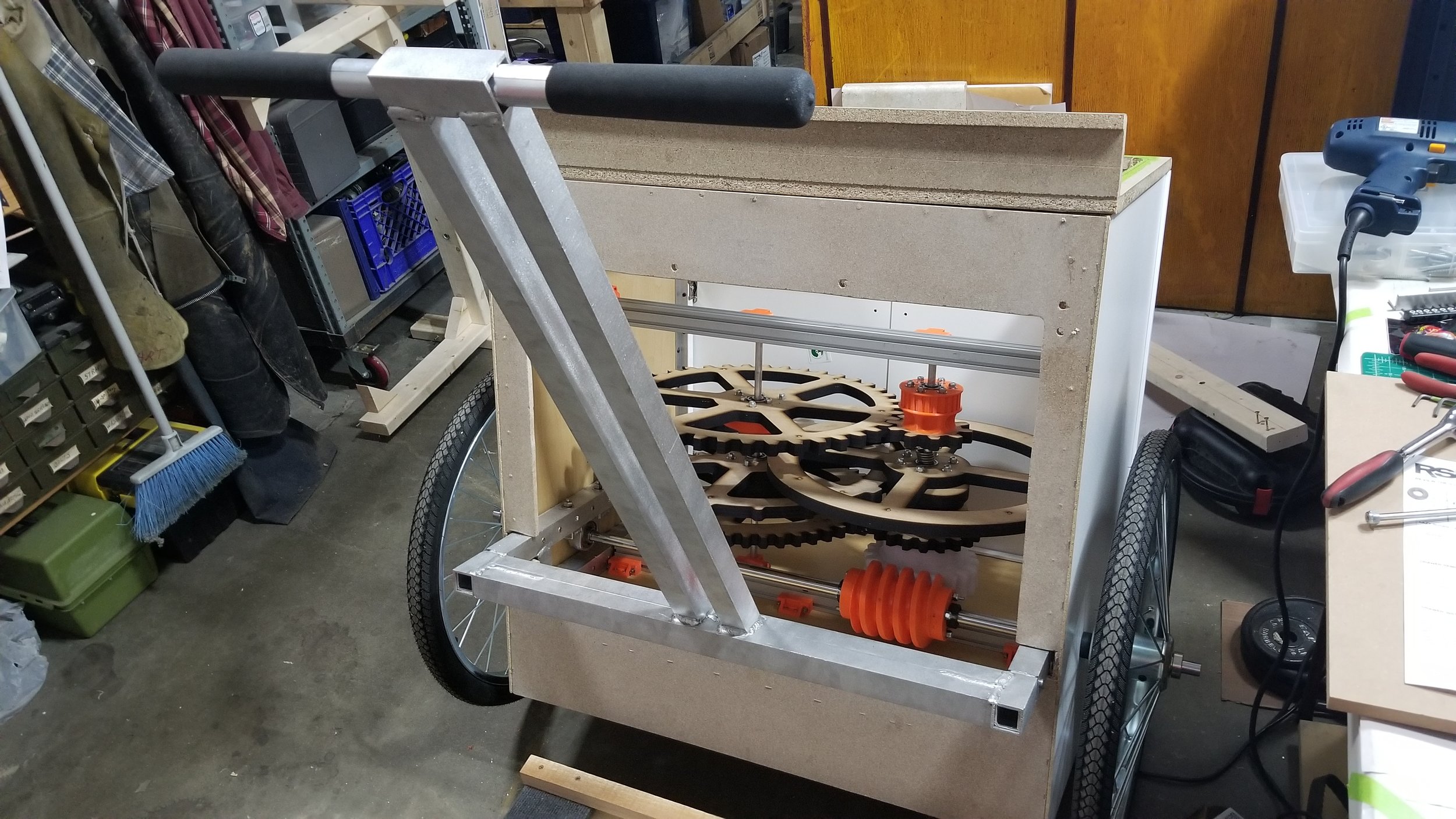
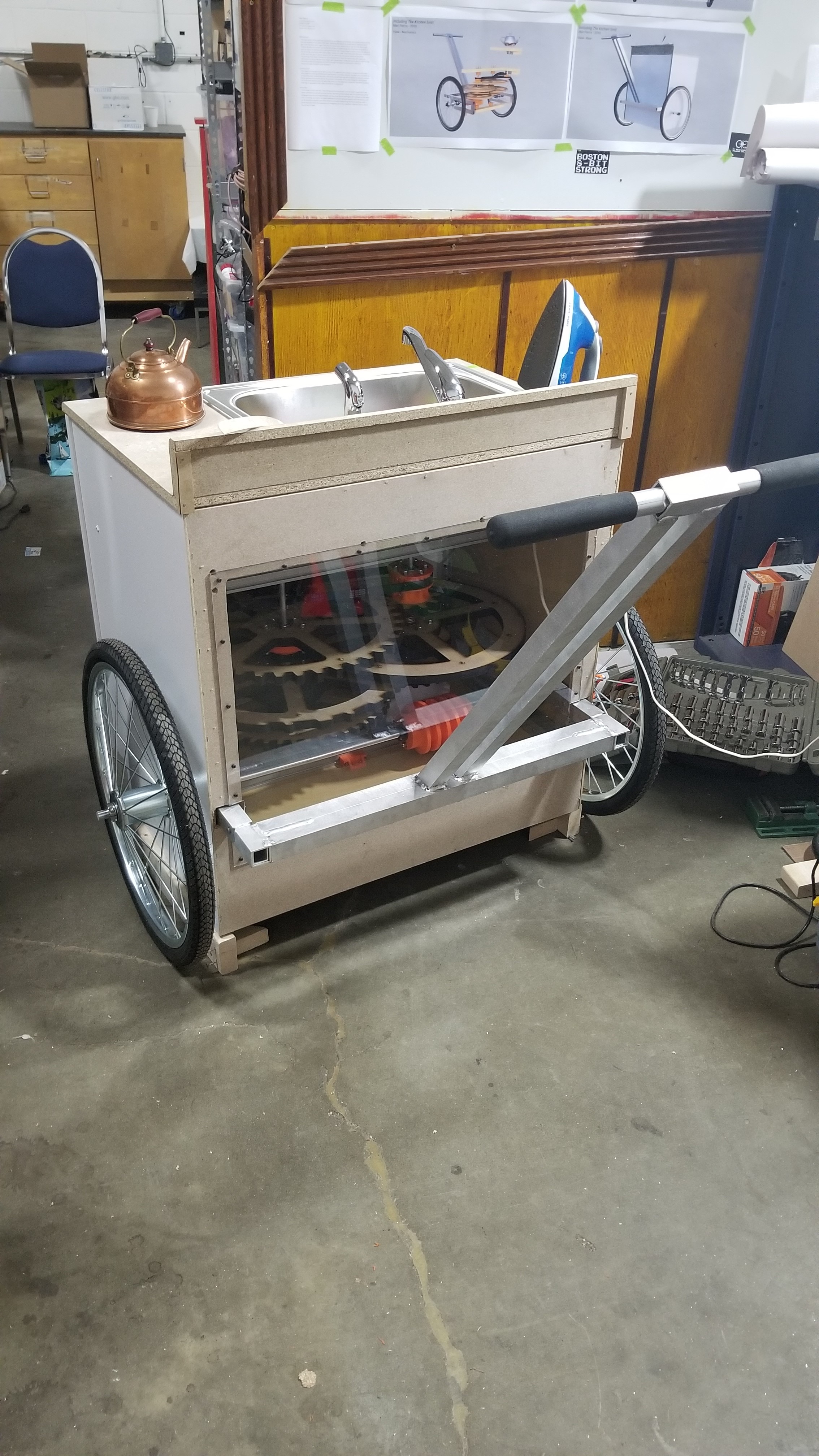
And from there it was mostly done.
RACEDAY !
At this point I’d been working on it for about 16 hours straight. Time to go run a race.
Look at that beauty!
One of the other Kinetic Sculpture Race contestants was at the asylum, so we carpooled it down to the race. The race itself was part of the larger Cambridge River Arts Festival, which took place in Cambridge MA on June 2nd, 2018.
“He even packed the kitchen sink!”
We made the trip easily, and after getting the organizational pieces out of the way, it was time.
Race Time.
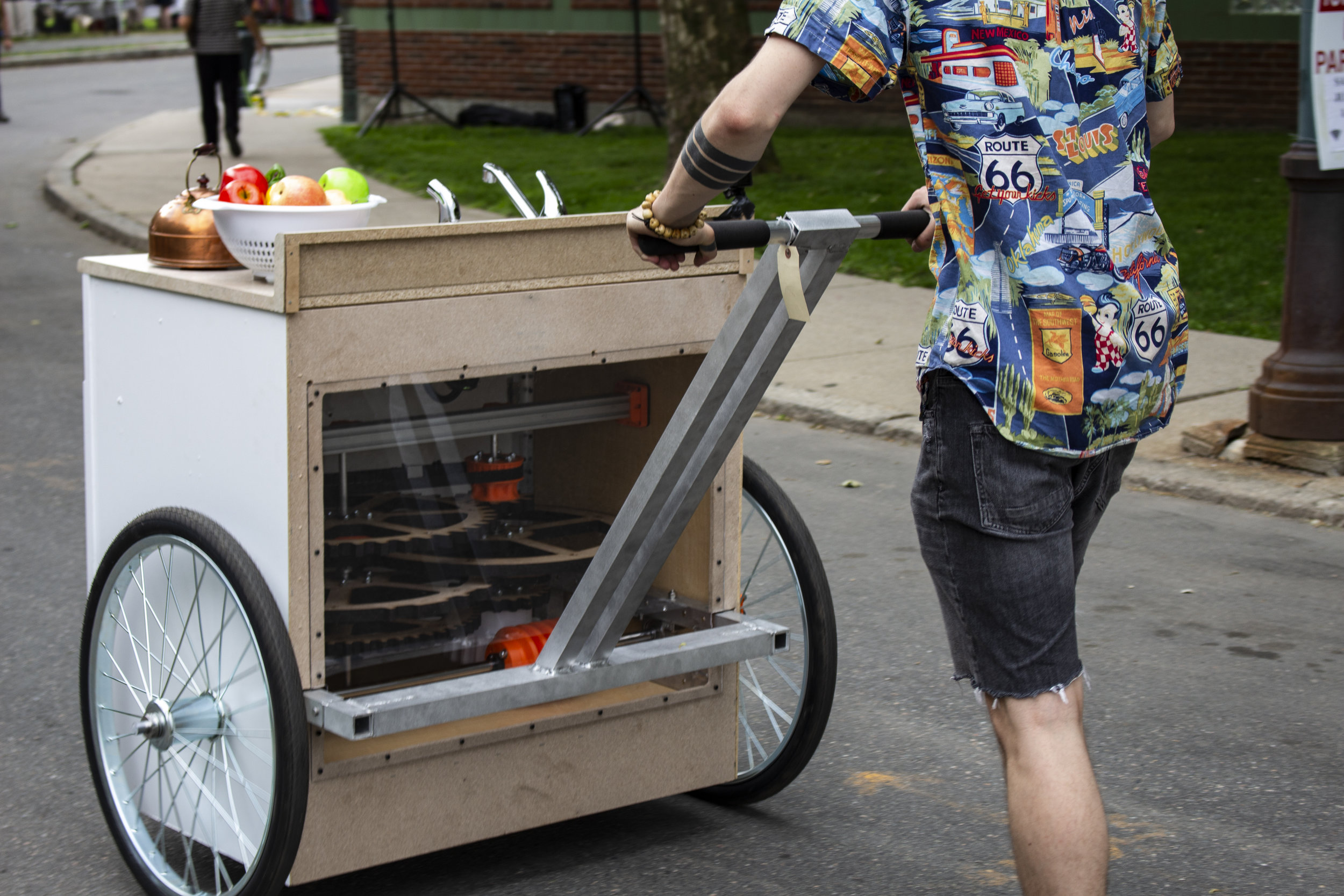
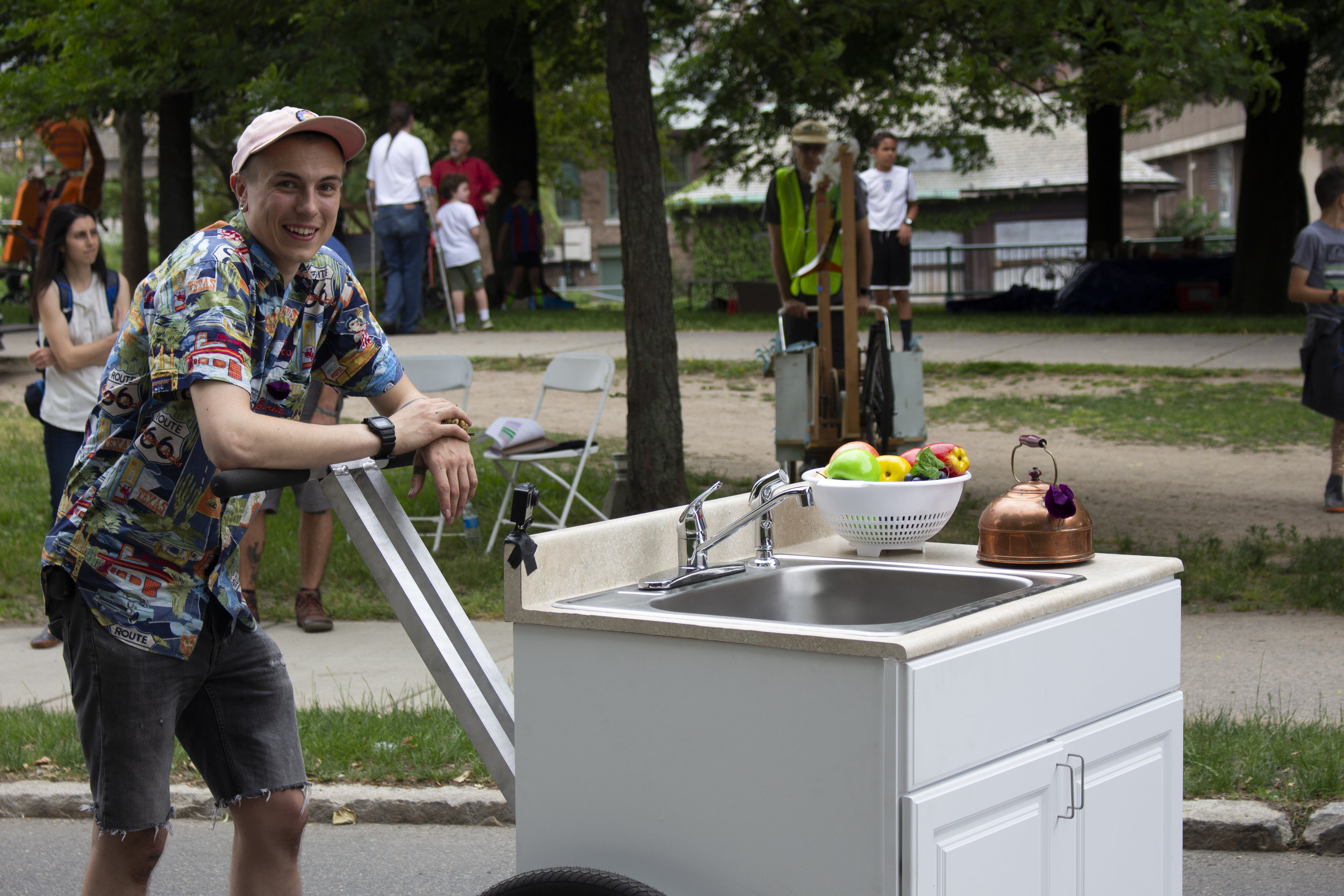
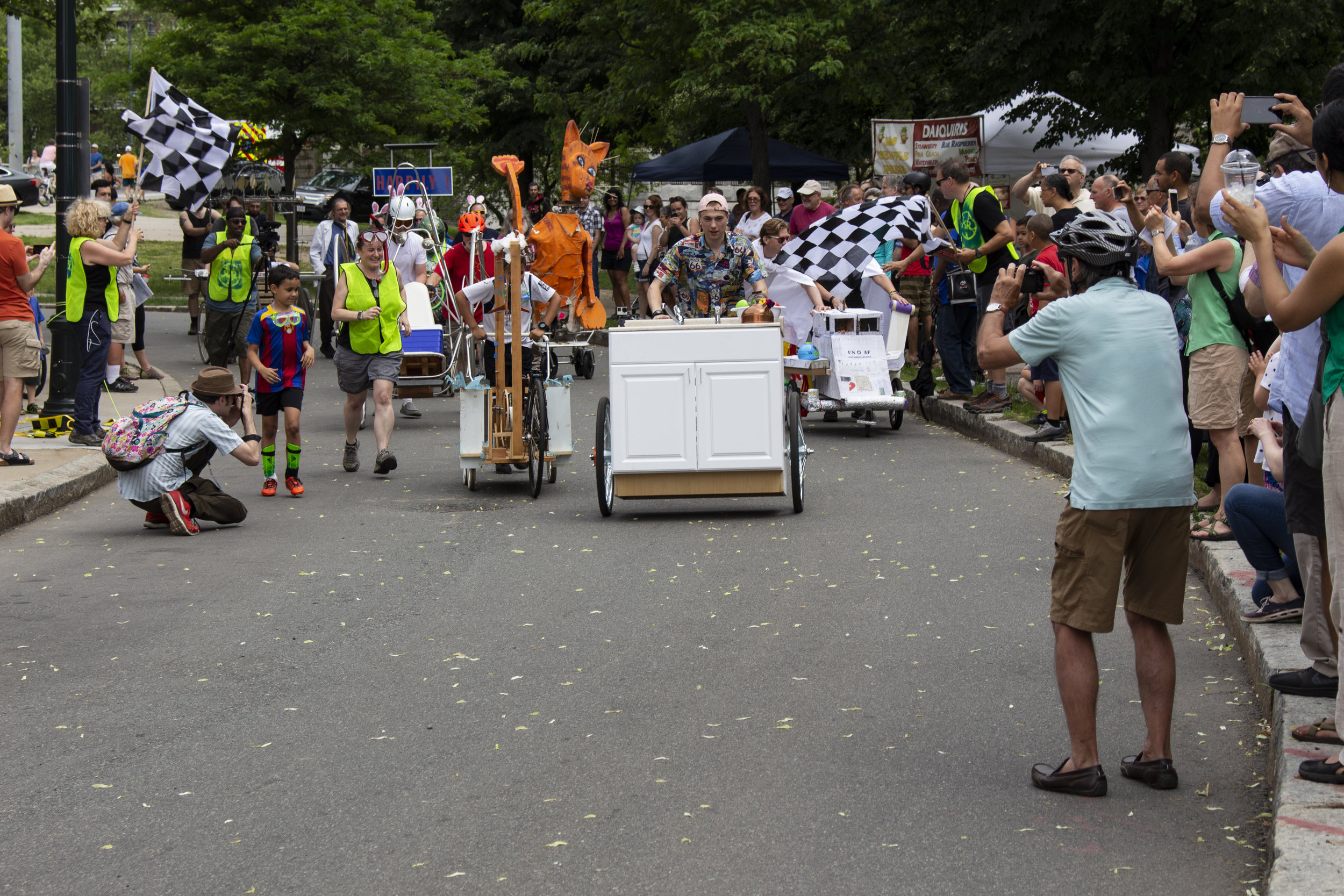
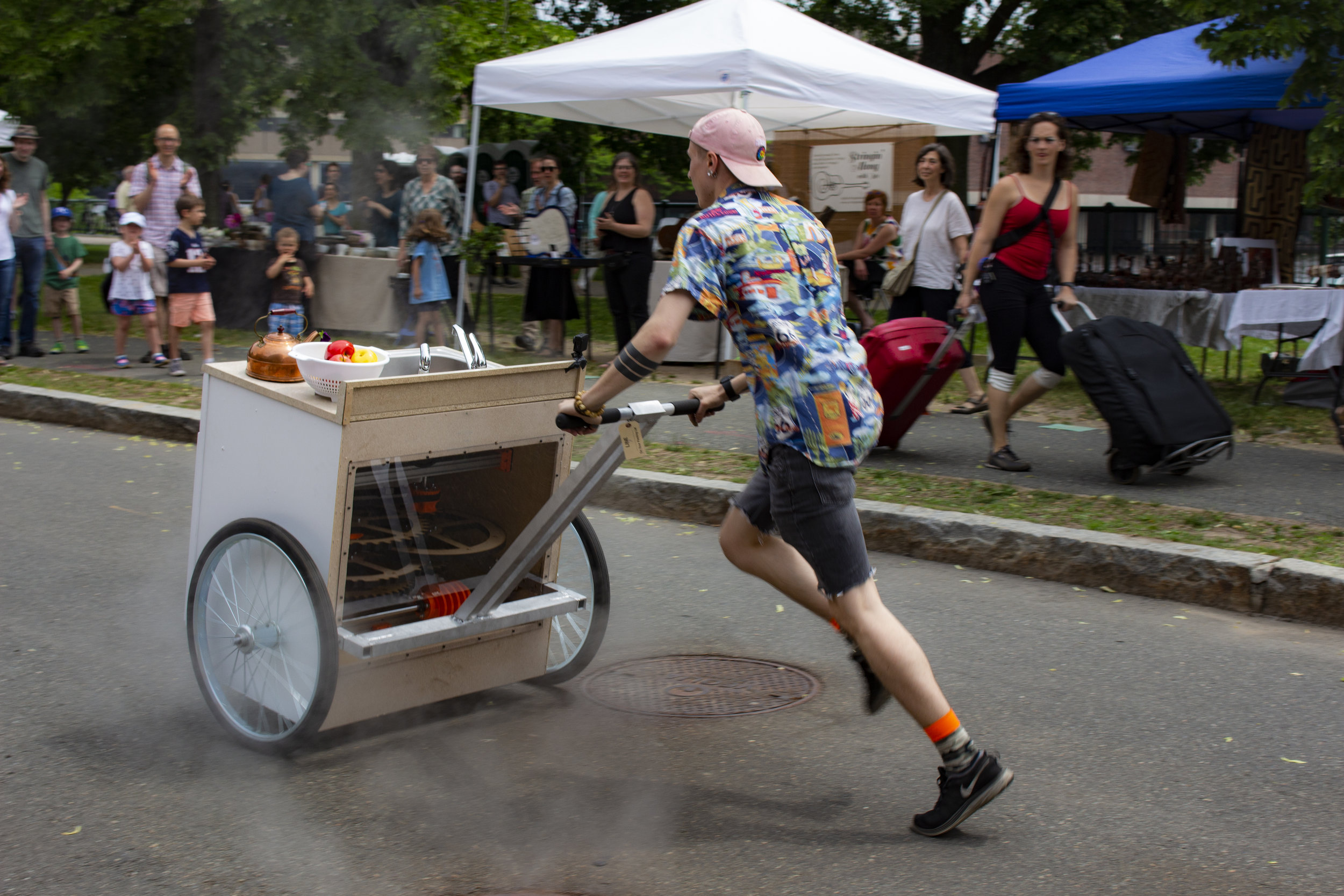
GO GO GO!
A few bumps along the way
FIRST!
All and all, Including the Kitchen Sink came in first for competed time, and took home the trophy for fastest racetime.
Man, what a fun time. 200 man-hours to build, less than 7 minutes to race.
10/10, would race again.